.png)
Smart factories are no longer a futuristic concept but a present reality that’s reshaping how we think about production, efficiency, and sustainability. These intelligent manufacturing environments are powered by an interconnected ecosystem of advanced technologies that work together seamlessly to create autonomous, adaptive, and highly efficient operations.
- Machine Learning
At the heart of smart factory management in 2025 lies machine learning. This technology has evolved far beyond simple automation to become the brain of modern manufacturing operations. Such systems now make autonomous decisions, optimize workflows in real-time, and continuously learn from every process to improve performance.
Machine learning algorithms are transforming predictive analytics by analyzing vast amounts of production data to forecast equipment failures before they happen. This predictive capability has revolutionized maintenance strategies, with manufacturers like Siemens reporting up to 30% faster time-to-market results.
- IoT
The Internet of Things and Industrial IoT serve as the nervous system of smart factory management, connecting every machine, sensor, and process into a unified network. This connectivity creates unprecedented visibility into manufacturing operations, allowing managers to monitor everything from equipment health to energy consumption in real-time.
IIoT sensors embedded throughout production lines generate continuous streams of data about machine performance, environmental conditions, and production metrics. This constant flow of information enables predictive maintenance strategies that can reduce unplanned downtime by up to 50% while cutting maintenance costs by 40%.
Companies like Caterpillar have successfully leveraged IoT technologies to create more agile manufacturing processes, achieving significant reductions in labor costs while improving product quality. The real-time monitoring capabilities allow for immediate responses to anomalies, preventing small issues from becoming major production disruptions.
Also Read: Factory Operation Management: Best Practices for Scaling Efficiently
- Robotics and Automation In Factories
Modern smart factory management relies heavily on advanced robotics and automation systems to handle complex manufacturing tasks with precision and consistency. Collaborative robots, or cobots, have become particularly valuable because they can work safely alongside human operators, combining the efficiency of automation with human creativity and problem-solving skills.
Tesla’s Gigafactories exemplify the power of integrated robotics in smart factory management. Their highly automated production lines have dramatically reduced vehicle assembly times while maintaining exceptional quality standards. This approach enables rapid scaling of production to meet growing demand without compromising safety or efficiency.
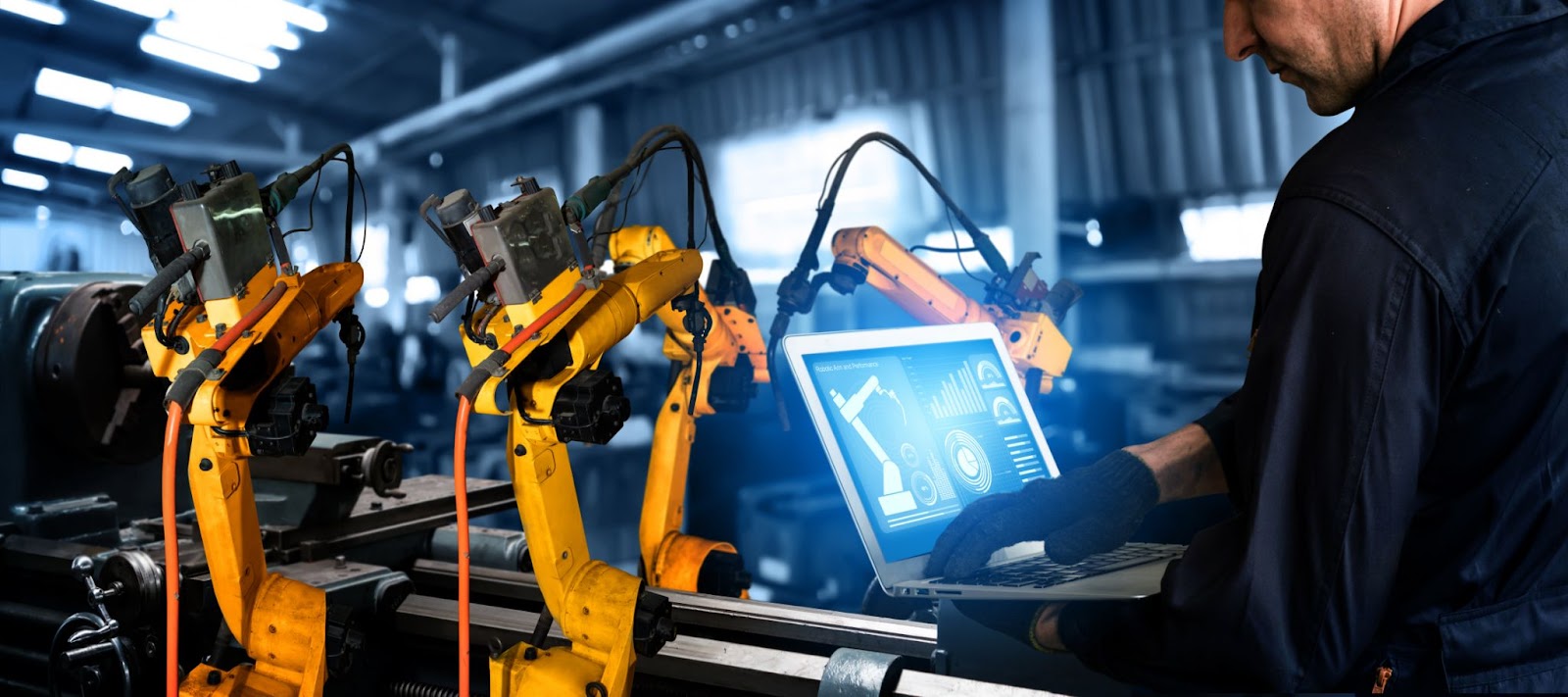
- Digital Twins
Digital twin technology represents one of the most exciting developments in smart factory management. By creating virtual replicas of physical assets, production lines, or entire factories, manufacturers can simulate and optimize processes before implementing changes in the real world.
This virtual testing environment allows engineers to experiment with different configurations, predict the impact of modifications, and identify potential problems before they affect actual production. The result is reduced downtime, improved product quality, and faster innovation cycles.
Siemens has been a pioneer in digital twin implementation, using these virtual models to optimize production processes and reduce energy consumption. Their success demonstrates how digital twins can deliver both operational improvements and sustainability benefits simultaneously.
Also Read: How a Factory Management System Can Cut Costs and Improve Productivity
- Edge and Cloud Computing
Smart factory management in 2025 requires a sophisticated computing infrastructure that combines the immediate responsiveness of edge computing with the scalability and analytical power of cloud platforms. Edge computing processes critical data right on the factory floor, enabling split-second decision-making for safety systems and quality control processes.
Meanwhile, cloud computing provides the massive storage and computational resources needed for big data analytics, machine learning model training, and centralized monitoring across multiple facilities. This hybrid approach ensures that smart factories can respond instantly to immediate needs while continuously improving through advanced analytics.
- Advanced Analytics
The vast amounts of data generated by smart factory systems would be meaningless without sophisticated analytics platforms to process and interpret them. Advanced analytics tools convert raw sensor data, production metrics, and operational information into actionable insights that drive continuous improvement.
Big data analytics platforms can identify patterns and trends that human operators might miss, uncovering opportunities for process optimization, cost reduction, and quality improvement. These insights enable data-driven decision-making at every level of the organization, from real-time adjustments on the production floor to strategic planning in the boardroom.
- Intelligent Quality Assurance
Smart factory management has revolutionized quality control through intelligent quality assurance systems that combine AI, machine learning, and advanced sensor technology. These systems can detect defects in real-time, predict quality issues before they occur, and automatically adjust processes to maintain optimal quality standards.
Samsung's smart factories demonstrate the power of AI-driven quality assurance, using computer vision and automated inspection systems to achieve higher yields and reduce human error. This proactive approach to quality management is moving manufacturers closer to the goal of zero-defect production.
- Predictive Maintenance
One of the most impactful applications of smart factory management technology is predictive maintenance. By analyzing vibration patterns, temperature readings, and historical performance data, machine learning algorithms can forecast equipment failures with remarkable accuracy.
This predictive capability transforms maintenance from a reactive cost center into a proactive value driver. Manufacturers can schedule maintenance activities during planned downtime, reduce spare parts inventory, and extend equipment lifespan—all while avoiding the costly disruptions of unexpected failures.
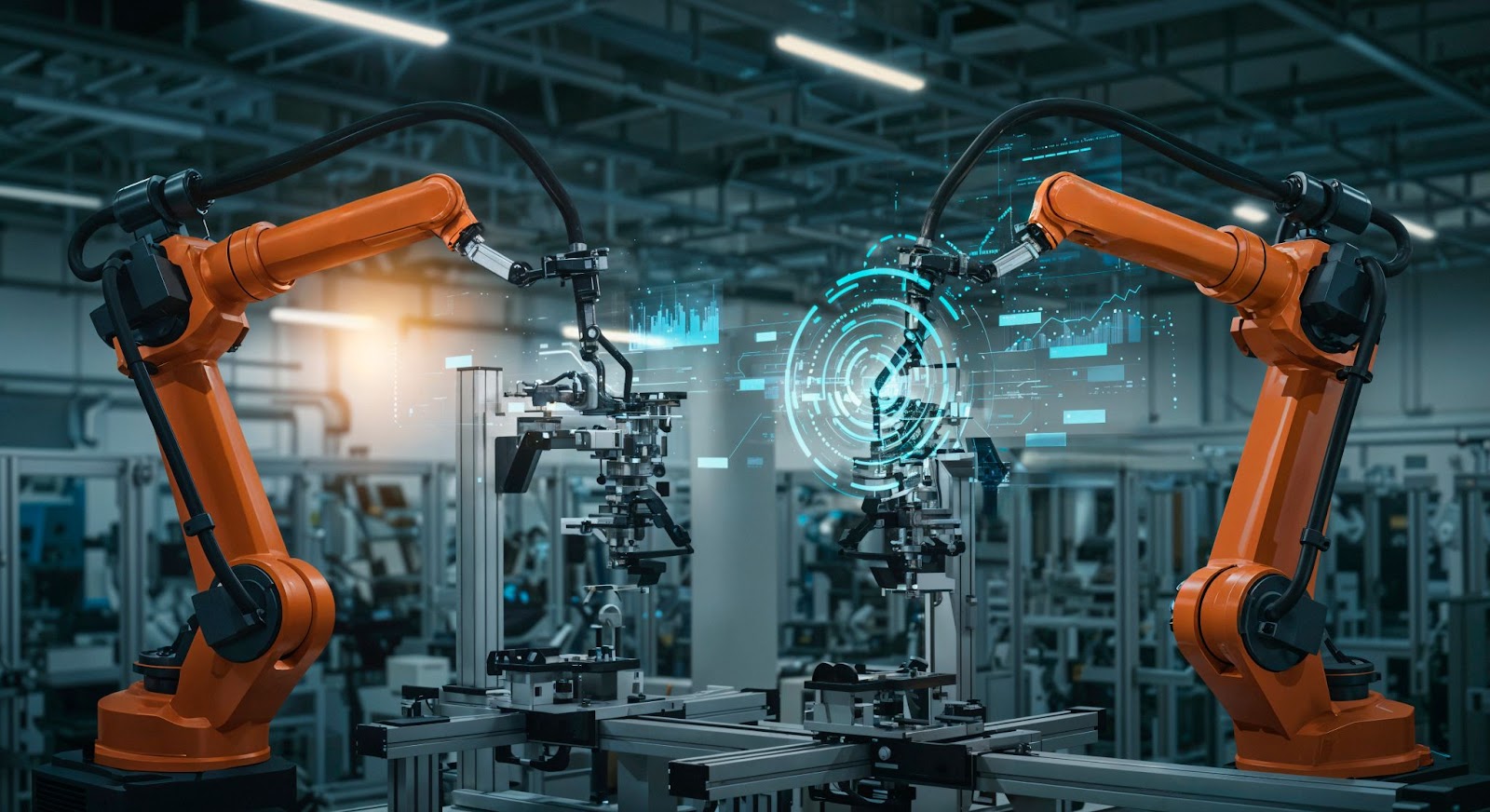
- Sustainability Technologies
Environmental responsibility has become a critical component of smart factory management in 2025. Companies like Toyota and Tata Steel have implemented comprehensive sustainability programs that include renewable energy integration, hydrogen fuel cells, and advanced recycling systems. These initiatives not only reduce environmental impact but also deliver significant cost savings and improve brand reputation.
Conclusion
As we look toward the future, smart factory management will continue evolving through the integration of emerging technologies and the refinement of existing systems. The key to success lies in understanding that these technologies work best when integrated into a cohesive ecosystem rather than implemented in isolation.