.jpg)
Staying ahead in the manufacturing landscape means finding smarter ways to operate. That's where factory management systems come in—they're revolutionizing how production facilities run by seamlessly integrating technology, data, and streamlined processes. If you're looking to boost your bottom line while ramping up output, implementing a comprehensive factory management solution might be exactly what your operation needs.
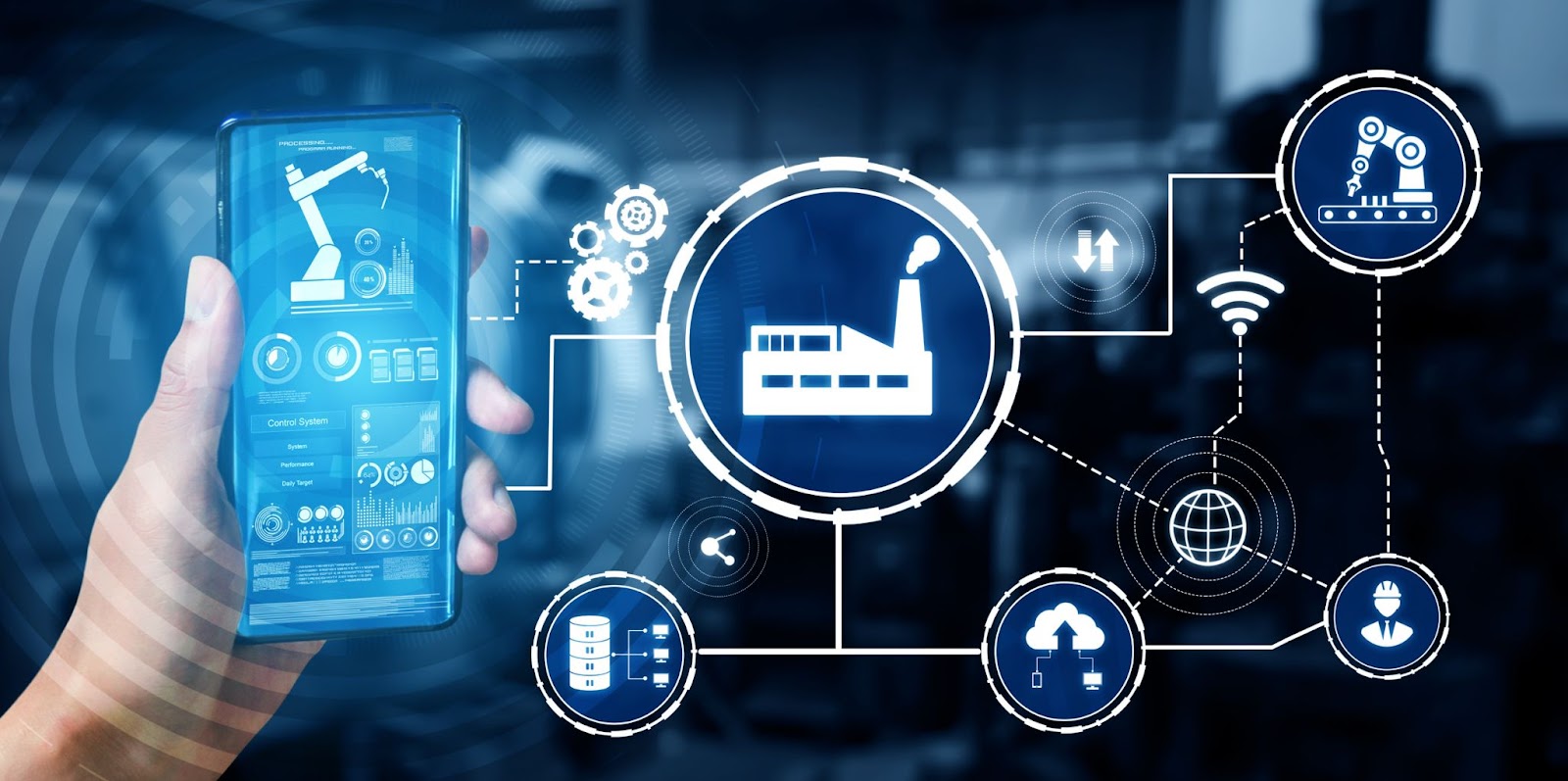
- Process Automation
One of the most immediate benefits of implementing a factory management system is the automation of tedious, repetitive tasks. Consider how much time your team spends on manual data entry, inventory checks, or quality control inspections.
Modern systems use robotic process automation to handle these tasks with greater speed and accuracy, contributing to overall process optimization. For instance, Mitsubishi adopted an AI solution through Intelligent Project Solutions and reduced trade document processing by 50%.
What’s particularly impressive is how these systems can identify production bottlenecks in real-time. When a slowdown occurs, the system doesn't just flag it—it can actually suggest or even implement workflow adjustments on the fly. This kind of dynamic response keeps production moving smoothly throughout the day.
- Maintenance Gets Smarter, Equipment Lasts Longer
If you've ever had to shut down production because of unexpected equipment failure, you know how costly downtime can be. Traditional calendar-based maintenance schedules often mean you're either maintaining equipment too frequently (wasting resources) or not often enough (risking breakdowns).
Factory management systems flip this approach on its head with predictive maintenance. Using IoT sensors that monitor equipment health markers like vibration, temperature, and sound patterns, these systems can predict when a machine is likely to fail before it happens.
This shift to reliability-centered maintenance means you're servicing equipment based on its actual condition rather than arbitrary timeframes. When a critical machine that would normally cost thousands in emergency repairs gets maintained before it breaks down, the savings add up quickly.
Also Read: How Smart Systems Simplify Time Tracking and Overtime Calculations
- Inventory and Supply Chain
Remember the last time you had too much inventory sitting around, tying up capital, or worse, not enough materials to fulfill orders? Factory management systems tackle this common challenge by integrating warehouse management with enterprise resource planning.
These systems use real-time data to optimize inventory levels, ensuring you have exactly what you need when you need it. By analyzing historical data alongside current market conditions, they can even improve demand forecasting accuracy. This means less money tied up in excess inventory and fewer delays due to stockouts.
Many manufacturers are seeing their inventory turnover ratios improve from 8 times annually to 12 or more through these just-in-time approaches. Better yet, with improved supplier coordination through connected systems, lead times have dropped by 15-30% for businesses using integrated platforms.
- Energy Efficiency
Factory management systems aren't just tracking your production—they're also monitoring your energy usage. Smart sensors throughout your facility can identify energy consumption patterns and pinpoint inefficiencies in machinery, lighting, HVAC systems, and more.
Simple changes, like installing motion-activated LED lighting systems, can reduce energy use by as much as 60%. Identifying and fixing compressed air leaks—a common and often overlooked issue in manufacturing—can save tens of thousands of dollars annually per facility.
When combined with lean manufacturing principles like the 5S methodology (Sort, Set in order, Shine, Standardize, Sustain), these systems help eliminate waste in materials, motion, and downtime. Many factories have cut their operational costs by up to 20% through these energy and waste reduction initiatives.
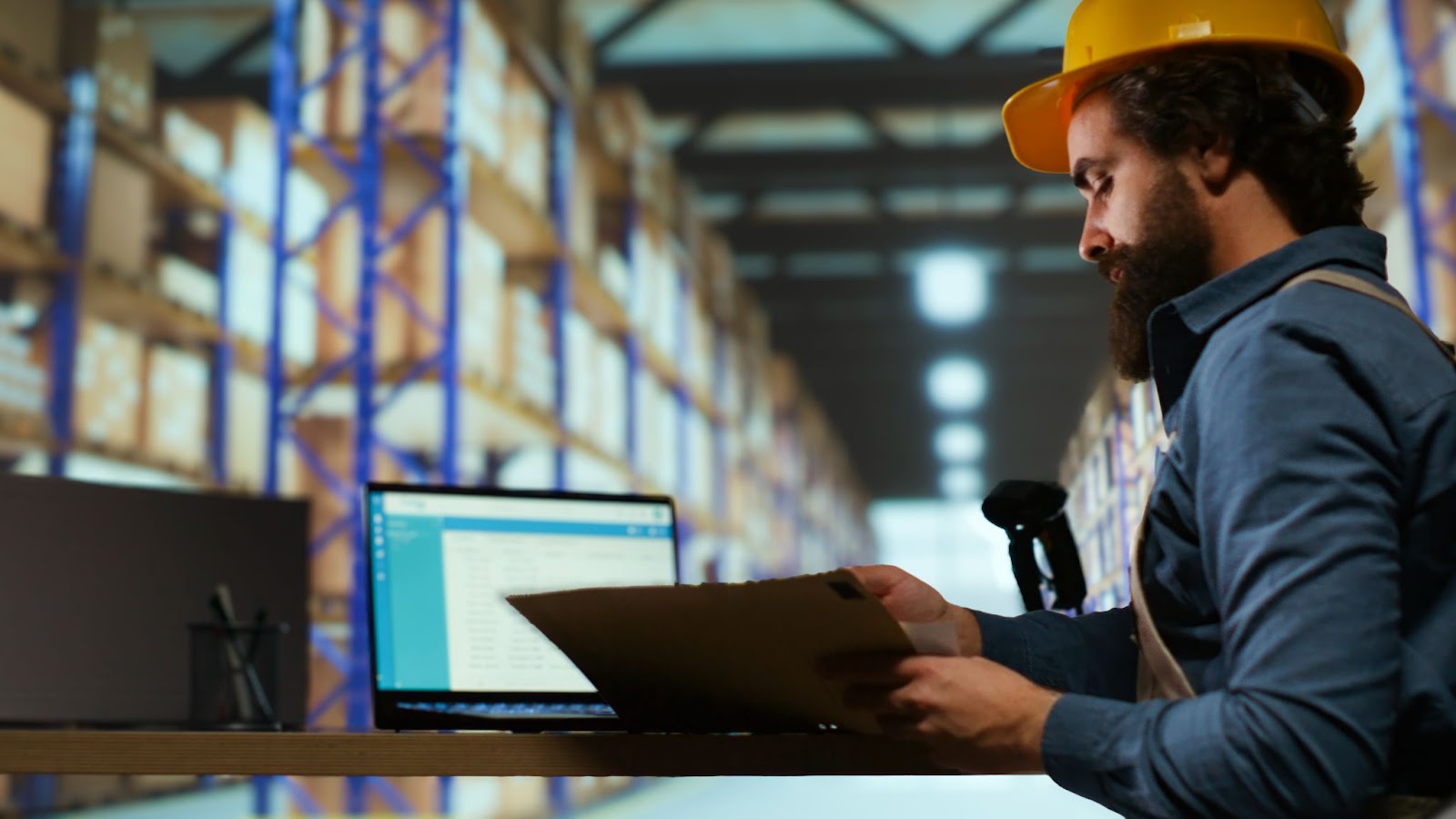
- Data-Driven Decisions
Perhaps the most transformative aspect of modern factory management systems is how they empower decision-making. Instead of relying on gut feelings or limited perspectives, managers get access to centralized dashboards showing real-time production metrics.
These platforms track critical KPIs like Overall Equipment Effectiveness (OEE), allowing teams to identify exactly where inefficiencies occur. When production falls below targets, AI-driven analytics can help determine the root causes—whether it's a training issue, equipment problem, or process bottleneck.
This approach also improves workforce development by highlighting specific skill gaps. Rather than generic training programs, teams can receive targeted instruction based on actual performance data, standardizing best practices across all shifts and production lines.
- Integrated Operations
Traditional factories often operate with disconnected systems—production doesn't talk to maintenance, and neither communicates effectively with inventory management. Modern factory management systems break down these silos by unifying operations “inside and outside the yellow line.”
For example, when maintenance schedules are synchronized with production demands through a unified platform, downtime is minimized. Shared AI inventory tools ensure parts are available exactly when maintenance needs them, preventing delays that would otherwise impact production schedules.
Also Read: How Project Management Solutions Improve Team Collaboration and Efficiency
- Employee Management System
Factory management systems and employee management tools now work together to improve productivity and lower costs. Real-time data helps optimize shift planning, cutting overtime and avoiding staff shortages. AI tools identify skill gaps, while AR-based training boosts learning speed and retention. These systems also track certifications to keep teams compliant and job-ready.
On the floor, live performance metrics and digital task instructions help workers stay efficient and accurate. Safety is enhanced through smart wearables, AI-powered monitoring, and real-time incident tracking, leading to fewer accidents and better compliance with safety standards.
Conclusion
Staying competitive means embracing systems that can simultaneously cut costs and boost productivity. A well-implemented factory management system accomplishes both by automating processes, preventing equipment failures, optimizing inventory, reducing energy waste, and empowering data-driven decisions.
Whether you're looking to reduce operational expenses, increase throughput, or improve product quality, a modern factory management system provides the tools to achieve these goals simultaneously rather than treating them as competing priorities.