.jpg)
There’s more than meets the eye when it comes to manufacturing. While the finished product is given the highest priority, an equal amount of importance is given to factory operation management as well. In this article, we’ll look at what this process is all about and some of the best practices for scaling efficiently.
What Is Factory Operation Management?
Factory Operation Management (FOM), sometimes called Manufacturing Operations Management (MOM), encompasses all the systems and processes needed to transform raw materials into finished products. It's the backbone of any successful manufacturing operation, connecting enterprise-level planning with shop floor execution.
The ultimate goal of MOM is to produce the highest quality of products at a lower cost, but as quickly and efficiently as possible. When done well, production improves, and inventory and staffing processes become smoother.
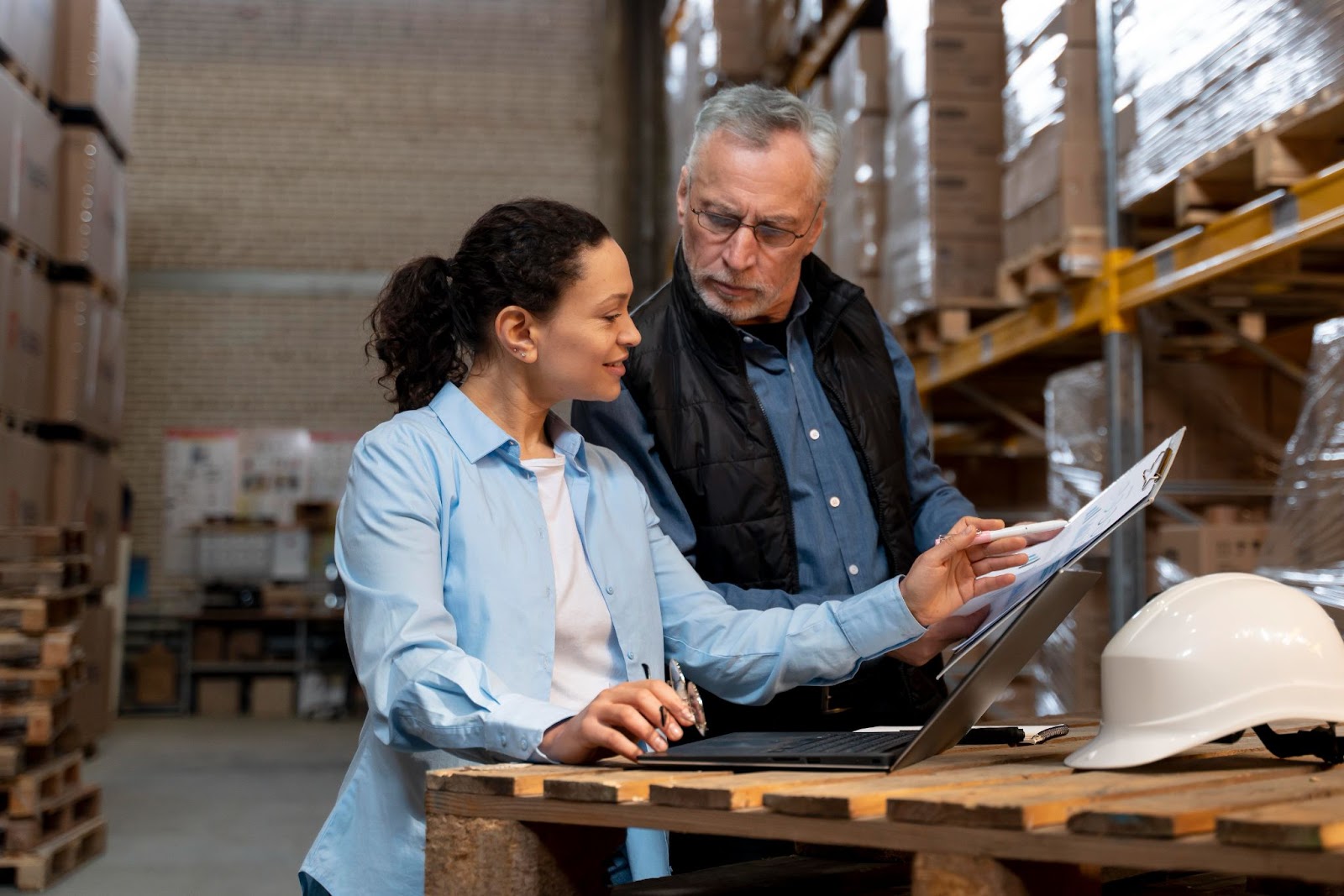
The Core Components of Effective Factory Management
At its heart, factory operation management relies on several interconnected systems:
- Production Planning and Scheduling: As your operation scales, the complexity of coordinating production increases exponentially. Advanced forecasting methods help anticipate demand fluctuations while master production schedules ensure resources align with business goals.
- Inventory Management: Scaling efficiently means having just enough inventory, not too much, not too little. Modern factory management employs real-time tracking systems to maintain optimal stock levels while reducing carrying costs.
- Quality Control: When scaling production, quality cannot be compromised. Embedded quality measures throughout the production process help identify issues before they become costly problems.
- Maintenance Management: Equipment reliability becomes even more crucial when scaling. Preventive and predictive maintenance strategies keep machinery running at peak performance, reducing costly downtime.
Also Read: 5 Reasons Your Business Needs Workforce Management Software
Best Practices for Scaling Factory Operations Efficiently
- Embrace Lean Manufacturing Principles in Manufacturing Process Optimization
Lean manufacturing focuses on eliminating waste in all forms—overproduction, waiting time, unnecessary transportation, excess inventory, and defects. When scaling your factory operations, these principles become even more important.
Value stream mapping helps visualize how materials and information flow through your facility, making it easier to identify bottlenecks that might hinder scaling efforts. The 5S methodology (Sort, Set in order, Shine, Standardize, Sustain) creates a more organized workspace that supports increased production volumes without chaos.
As production scales, Just-in-Time (JIT) inventory practices help keep inventory costs manageable while ensuring materials are available when needed. Continuous improvement (Kaizen) creates a culture where small, regular enhancements add up to significant gains in capacity and efficiency.
- Leverage Technology for Smarter Operations
Technology integration forms the foundation of scalable factory operation management. Manufacturing Execution Systems (MES) provide real-time visibility into production processes, enabling managers to make data-driven decisions quickly.
The Industrial Internet of Things (IIoT) connects machines and equipment, generating valuable data that helps optimize operations. Smart sensors monitor equipment health, product quality, and production rates, providing early warning of potential issues before they disrupt scaled operations.
Advanced analytics transforms raw data into actionable insights, helping identify patterns and optimization opportunities that might otherwise go unnoticed. Automation of repetitive tasks not only increases throughput but also maintains consistency as production scales.
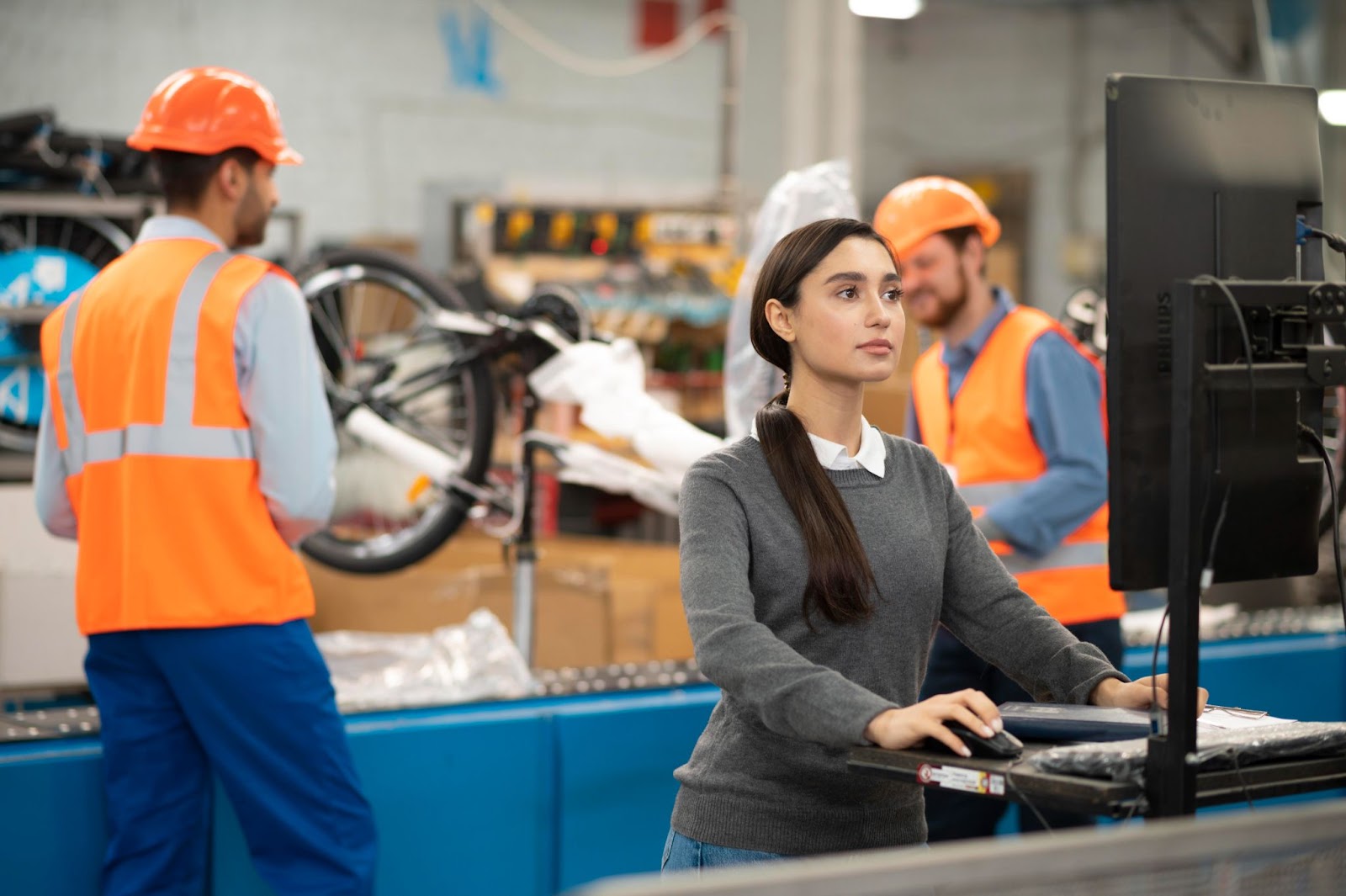
- Optimize Your Workforce Strategy
People remain at the heart of successful factory operation management, even in increasingly automated environments. As operations scale, workforce development becomes a critical factor.
Cross-training employees creates flexibility, allowing team members to step into different roles as production needs fluctuate. Clear communication channels ensure that everyone understands their responsibilities and how they contribute to the larger operation.
Employee engagement initiatives help maintain morale and productivity during scaling phases. Performance metrics tied to operational goals keep everyone focused on what matters most.
Also Read: How Smart Systems Simplify Time Tracking and Overtime Calculations
- Implement Robust Supply Chain Integration
Scaling factory operations requires synchronized supply chain management. Close collaboration with suppliers ensures material availability matches production demands.
Vendor-managed inventory systems can reduce the administrative burden while maintaining appropriate stock levels. Digital supply chain platforms improve visibility across the entire network, helping anticipate and address potential disruptions before they impact production.
Regular supplier performance reviews ensure that your partners can scale alongside your operations. Risk management strategies identify alternative sourcing options to protect against supply interruptions.
Measuring Success in Factory Operation Management
Scaling efficiently requires clear metrics to track progress and identify areas for improvement:
- Overall Equipment Effectiveness (OEE) measures availability, performance, and quality, providing insight into how well your equipment supports scaling efforts.
- Cycle time indicates how quickly products move through your production process. As you scale, maintaining or improving cycle times becomes increasingly challenging yet critical.
- First Pass Yield tracks the percentage of products that meet quality standards without rework. This metric helps ensure that scaling doesn't come at the expense of quality.
- Inventory turnover shows how efficiently you're managing stock levels relative to production volume. Efficient scaling should maintain or improve this ratio.
Conclusion
Successful factory operation management isn't just about doing more—it's about doing more efficiently. By embracing lean principles, leveraging technology, optimizing workforce strategies, and integrating supply chains, manufacturers can scale operations without proportionally increasing costs or complexity.
The journey toward scalable factory operations is continuous. Regular assessment of processes, technology, and people ensures that your manufacturing operation remains agile and responsive, ready to grow without sacrificing quality or efficiency.
As you implement these best practices in factory operation management, remember that scaling is not a destination but a process of continuous improvement and adaptation. The most successful manufacturers embrace this reality, creating systems that support growth while maintaining the operational excellence that drives competitiveness in today's manufacturing landscape.