.png)
Running a factory smoothly isn't just about having the right machines and workers—it's about orchestrating a complex symphony of moving parts that need to work in perfect harmony. If you're a factory manager or operations leader, you know firsthand that every day brings new challenges that can make or break your production goals.
The good news? Most factory operation management challenges are surprisingly common, which means proven solutions already exist. Let's dive into the most pressing issues facing modern manufacturing facilities and explore practical ways to tackle them head-on.
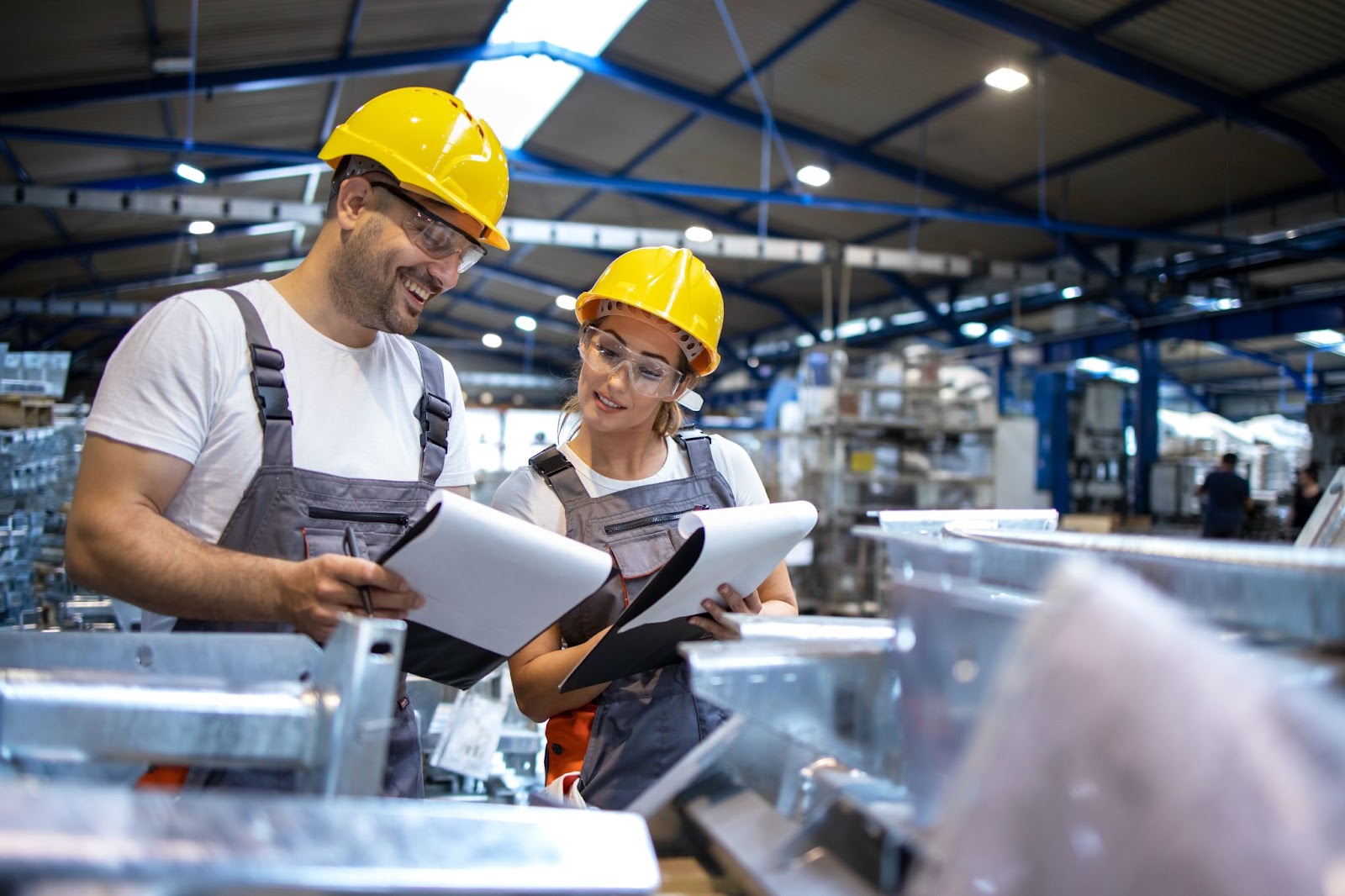
- Equipment Downtime
One of the most frustrating challenges in factory operation management is unexpected equipment breakdowns. Picture this: your production line is humming along perfectly when suddenly a critical machine stops working. Within minutes, you're looking at delayed orders, frustrated customers, and mounting repair costs.
Traditional reactive maintenance approaches simply don't cut it anymore. Smart factories are shifting toward predictive maintenance strategies that use IoT sensors and real-time monitoring to catch problems before they become disasters. By analyzing equipment performance data, you can schedule maintenance during planned downtime rather than scrambling to fix broken machines during peak production hours.
The key is training your operators to recognize early warning signs and creating a culture where reporting potential issues is valued, not feared. Regular maintenance schedules might seem like an unnecessary expense, but they’re one of the best investments you can make in your factory's long-term productivity.
- Operational Inflexibility
Many factories struggle with rigid systems that can't adapt quickly to changing demands. When market conditions shift or customer requirements evolve, inflexible operations become a major liability. This challenge in factory operation management often stems from outdated processes and disconnected systems that make rapid adjustments nearly impossible.
The solution lies in embracing flexible manufacturing systems and digital transformation. Modern ERP systems provide real-time visibility across your entire operation, allowing you to quickly pivot production schedules, reallocate resources, and respond to urgent orders. Automation doesn't just reduce labor costs—it also creates the flexibility to handle varying production volumes without major disruptions.
- Labor Costs and Skills Shortages
The manufacturing industry faces a perfect storm of rising labor costs and shrinking pools of skilled workers. This dual challenge in factory operation management forces many facilities to operate with understaffed teams while paying premium wages for experienced operators.
Rather than fighting this trend, successful manufacturers are getting creative with their approach to workforce development. Cross-training programs help create versatile employees who can handle multiple roles, reducing dependence on specialized workers. Automation can take over repetitive or dangerous tasks, allowing human workers to focus on higher-value activities that require problem-solving and decision-making skills.
Creating a culture of continuous improvement not only helps retain good employees but also ensures your team stays current with evolving technology and best practices. Digital training platforms make it easier than ever to provide ongoing education without disrupting production schedules.
- Inventory and Supply Chain Complexity
Poor inventory management is like having a slow leak in your profitability bucket. Too much inventory ties up cash and increases storage costs, while too little inventory leads to production stoppages and missed deliveries. Add supply chain disruptions to the mix, and inventory management becomes one of the trickiest aspects of factory operation management.
Advanced inventory management systems integrated with ERP software provide the real-time visibility needed to optimize stock levels. These systems can automatically trigger reorders based on actual consumption patterns rather than guesswork, dramatically reducing both shortages and excess inventory.
Demand forecasting tools that analyze historical data alongside market trends help align inventory levels with actual business needs. The goal isn't to eliminate all inventory risk but to find the sweet spot between availability and cost efficiency.
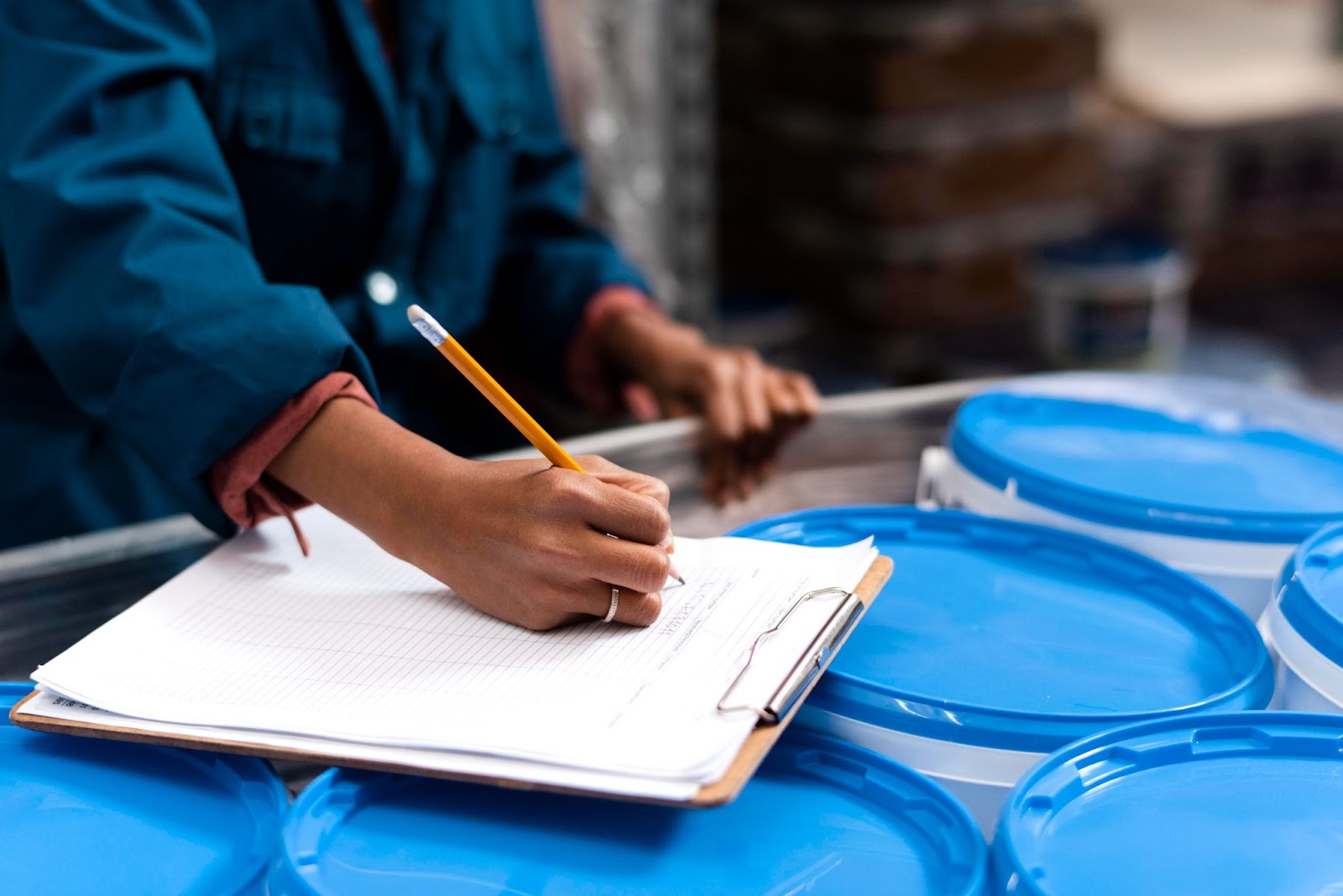
- Production Bottlenecks and Capacity Constraints
Every factory has that one process or machine that seems to slow everything down. These bottlenecks in factory operation management create cascading delays that affect the entire production line and ultimately disappoint customers.
Identifying bottlenecks requires careful analysis of production data and workflow patterns. Sometimes the solution is as simple as redistributing workload or adjusting shift schedules. Other times, it might require equipment upgrades or process redesign.
Lean manufacturing principles provide excellent frameworks for identifying and eliminating waste in production processes. Scheduling software can help optimize resource allocation and workflow management to minimize idle time and maximize throughput.
- Quality Control and Compliance in Modern Manufacturing
Maintaining consistent product quality while meeting increasingly complex regulatory requirements presents ongoing challenges in factory operation management. Manual quality checks are time-consuming and prone to human error, while regulatory compliance demands detailed documentation and traceability.
Standardizing procedures using methodologies like Six Sigma creates reproducible processes that naturally improve quality outcomes. Manufacturing execution systems can automate many quality checks and maintain the detailed records required for compliance audits.
The 5S methodology—Sort, Set in Order, Shine, Standardize, and Sustain—helps create organized workspaces where quality issues become immediately visible, making prevention much easier than correction.
- Smart Cost Management and Overhead Reduction
Controlling costs without sacrificing quality or safety requires a strategic approach to factory operation management. Every expense needs justification, but cutting costs in the wrong places can create bigger problems down the road.
Monitoring key performance indicators provides objective data for cost management decisions. Automation can reduce routine operational expenses while improving consistency and reducing errors. Lean practices help identify and eliminate wasteful processes that add cost without adding value.
The most successful cost reduction efforts focus on improving efficiency rather than simply cutting expenses. When processes become more efficient, costs naturally decrease while quality and customer satisfaction improve.
- Safety and Risk Management
Safety isn't just about compliance—it's fundamental to efficient factory operation management. Workplace injuries disrupt production, increase costs, and damage morale. Beyond physical safety, operational risks like equipment failures, supply disruptions, and quality issues can threaten business continuity.
Creating a strong safety culture starts with leadership commitment and regular training programs. Standardized procedures and clear protocols help ensure consistent, safe practices across all shifts and departments.
Risk management strategies should identify potential threats before they materialize and establish contingency plans for various scenarios. Regular risk assessments help keep these plans current and relevant.
Conclusion
Successfully addressing these common challenges in factory operation management requires an integrated approach that combines technology adoption, process optimization, and workforce development. No single solution addresses all challenges, but the right combination of strategies can transform factory operations from reactive firefighting to proactive management.