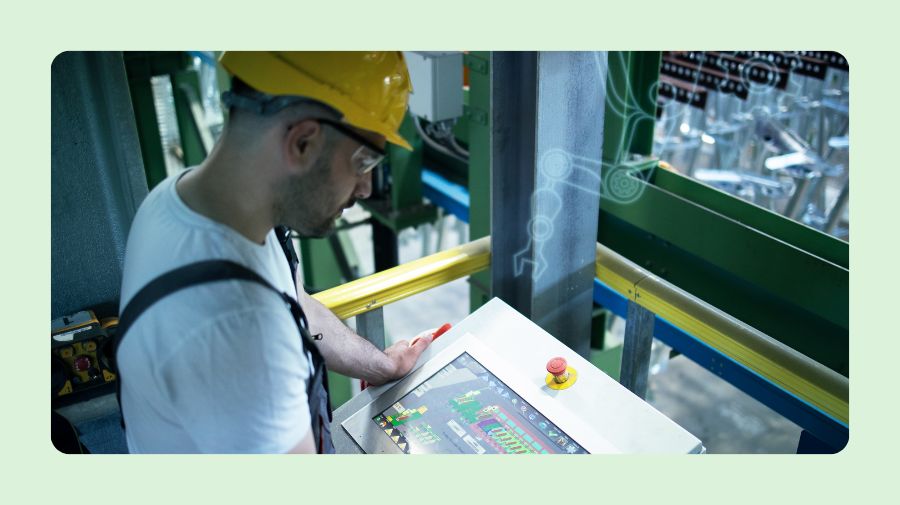
Smart factory technology is transforming the way products are designed, produced, and delivered. This digital revolution combines cutting-edge technologies like IoT, AI, and robotics to create manufacturing environments that are more connected, efficient, and responsive than ever before.
Let's explore how these intelligent systems are reshaping the manufacturing sector and delivering unprecedented benefits.
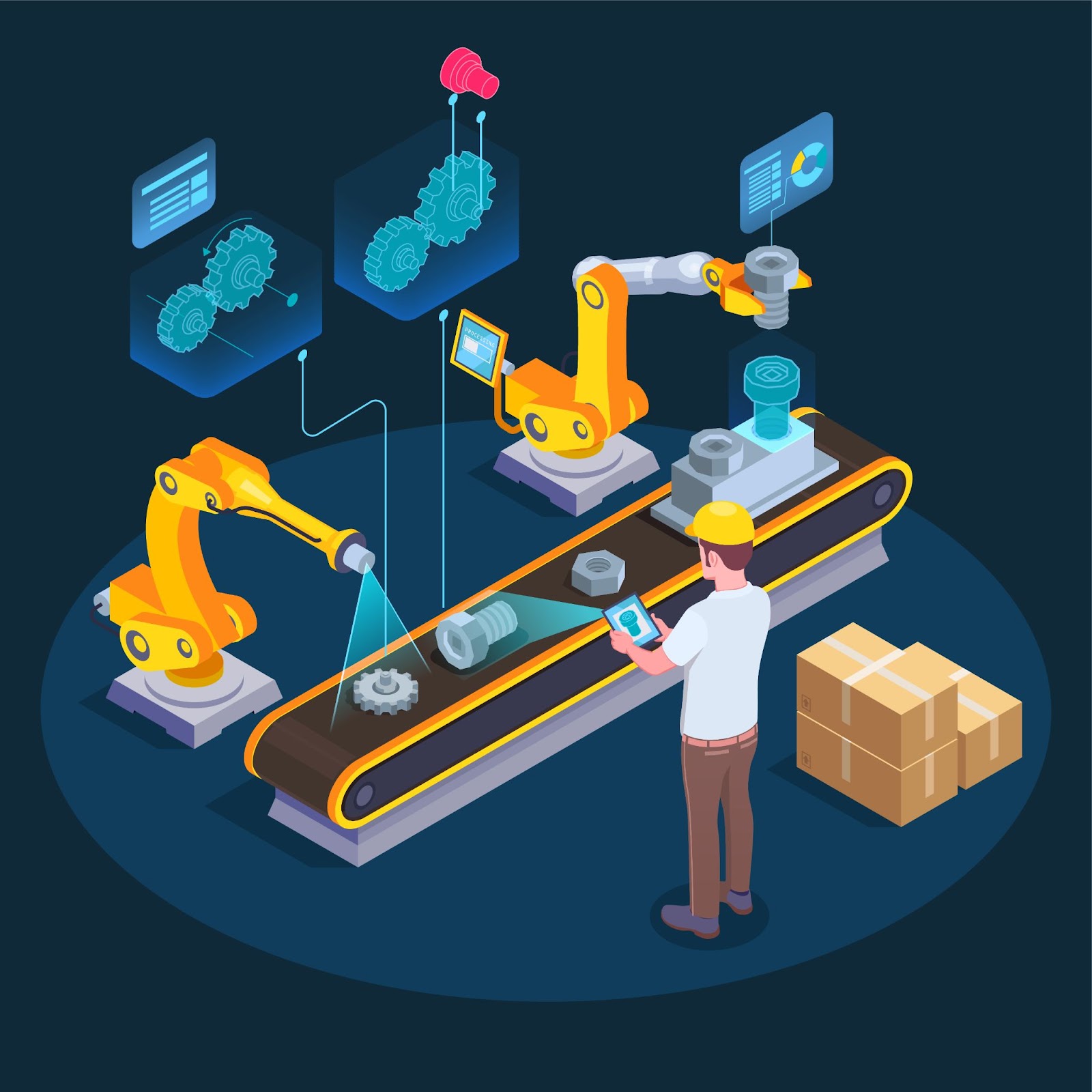
The Digital Transformation In Manufacturing
Smart factory management represents a fundamental shift from traditional manufacturing approaches. Smart factories leverage interconnected sensors, real-time data analytics, and automated decision-making to create a seamless, self-optimizing production environment.
These intelligent factories continuously collect data from equipment, materials, and processes, transforming this information into actionable insights. This allows manufacturers to identify inefficiencies, predict maintenance needs, and make data-driven decisions that boost productivity and reduce costs.
Enhancing Efficiency Through Predictive Capabilities
One of the most significant advantages of smart factory management is the move from reactive to proactive operations. Rather than waiting for machines to break down or quality issues to emerge, smart factories can anticipate problems before they occur.
IoT sensors embedded in equipment monitor parameters like temperature, vibration, and performance metrics in real-time. When these sensors detect anomalies that might indicate an impending failure, the system can automatically schedule maintenance during planned downtime, preventing costly production interruptions.
For example, a bearing showing unusual vibration patterns might signal potential failure. In a smart factory, this would trigger an alert, allowing technicians to replace the part before a breakdown occurs. This predictive approach dramatically reduces unplanned downtime, extends equipment lifespan, and optimizes maintenance resources.
Revolutionizing Quality Control
Smart factory management has transformed quality assurance from a post-production checkpoint to an integrated, continuous process. Advanced vision systems and AI-powered inspection tools monitor products throughout the manufacturing process, detecting defects with greater accuracy and consistency than human inspectors.
These systems can identify issues like dimensional inaccuracies, surface flaws, or assembly errors in real-time. When problems are detected, the system can immediately alert operators or automatically adjust machine settings to correct the issue, preventing defective products from moving further down the production line.
An exemplary case is that of John Deere, a manufacturer specializing in landscaping machinery. He leveraged Intel’s AI technology to detect welding defects in manufacturing even more accurately than a qualified technician. This factory management tool used computer vision and neural network-based inference engines to identify anomalies in real-time. And once a defect was detected, it stopped the welding process and deployed immediate corrective actions.
The result? The company saved lots of time, money, and resources.
Also Read: 5 Reasons Your Business Needs Workforce Management Software
Creating Flexible and Customizable Production
Modern consumers increasingly demand personalized products, challenging the traditional mass production model. Smart factory management enables manufacturers to meet this demand through flexible, reconfigurable production systems.
Modular equipment and programmable robotics can quickly switch between different product variants with minimal downtime. Digital twins—virtual replicas of physical assets and production processes—allow manufacturers to simulate changes and optimize configurations before implementing them on the factory floor.
Great Wall Motor’s Smart Car Factory in Rayong, Thailand, is a modern facility that plays an important role in GWM’s global growth and advanced manufacturing efforts in Southeast Asia.
The factory uses intelligent robots, automated guided vehicles (AGVs), and a digital system called MES to streamline assembly and maintenance. It also runs advanced simulations in its welding area, allowing it to build various types of vehicles—like hybrids, plug-in hybrids, electric cars, and regular fuel-powered ones—on the same line.
Even with just around 70 workers on the production line, the plant can turn out about 200 cars a day. Robots handle 84% of the welding work, and AI tools help boost both the speed and quality of production.
Driving Sustainability and Resource Optimization
As environmental concerns grow, smart factory management is helping manufacturers reduce their ecological footprint, making it one of the most important smart factory trends. Intelligent energy management systems monitor consumption in real-time and optimize usage by scheduling energy-intensive processes during off-peak hours or adjusting machine operation to reduce waste.
Rockwell Automation’s Asia Pacific manufacturing facility in Singapore is a good example of driving sustainability and resource optimization in smart factories. Their strategy relies on real-time monitoring, predictive analytics, and process improvements to boost efficiency and reduce waste.
A key part of this is the FactoryTalk Energy Manager—an AI-powered platform that gives the team live updates on how much energy different parts of the plant are using. From entire production areas down to individual machines, the system helps spot problems like air leaks early on so they can be fixed quickly.
The facility also uses predictive analytics and prescriptive controls to stay ahead of energy demand. Machine learning tools study past and current data to forecast changes and automatically tweak production settings to save power.
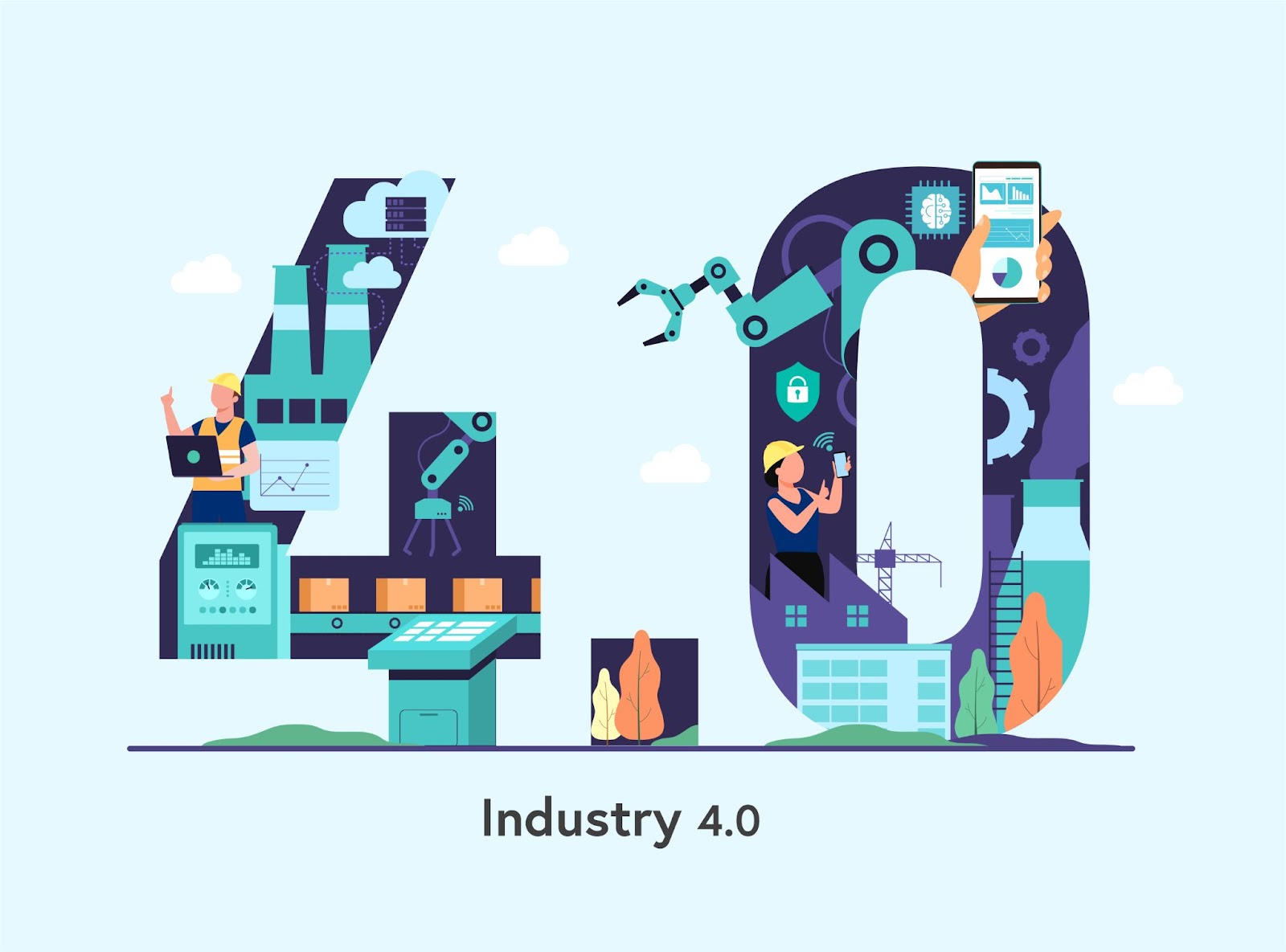
Transforming the Worker Experience
Contrary to popular belief, smart factory management isn't about replacing humans with machines. Instead, it's about creating safer, more engaging work environments where technology handles repetitive or dangerous tasks, freeing workers to focus on higher-value activities.
Automation of hazardous tasks reduces workplace injuries, while wearable devices and environmental sensors monitor worker safety conditions. Augmented reality tools assist with complex maintenance procedures, enhancing skills and reducing errors.
This technology-human partnership creates more rewarding roles that emphasize problem-solving, innovation, and strategic thinking rather than repetitive manual labor.
Also Read: How Smart Systems Simplify Time Tracking and Overtime Calculations
Building Resilient Supply Chains
Smart factory management extends beyond the factory floor to create more transparent and resilient supply chains. Digital platforms connect suppliers, manufacturers, distributors, and customers, providing real-time visibility into inventory levels, production status, and demand forecasts.
This end-to-end transparency enables manufacturers to respond quickly to disruptions, adjust production schedules dynamically, and maintain efficient operations even during challenging times. The COVID-19 pandemic highlighted the value of this capability, as manufacturers with digitally integrated supply chains were better able to adapt to sudden changes in demand and supply.
Conclusion
As we look toward the future, smart factory management will continue to evolve, incorporating new technologies and approaches. The emergence of Industry 5.0 emphasizes even greater human-machine collaboration, where robots and humans work together to create customized products with both precision and creativity.
Artificial intelligence capabilities will advance, potentially enabling factories to self-optimize and innovate autonomously. Sustainability will become more deeply integrated, with factories designed to be carbon-neutral and circular from the ground up.